Case Studies
Risk Management in Product Development and Manufacturing
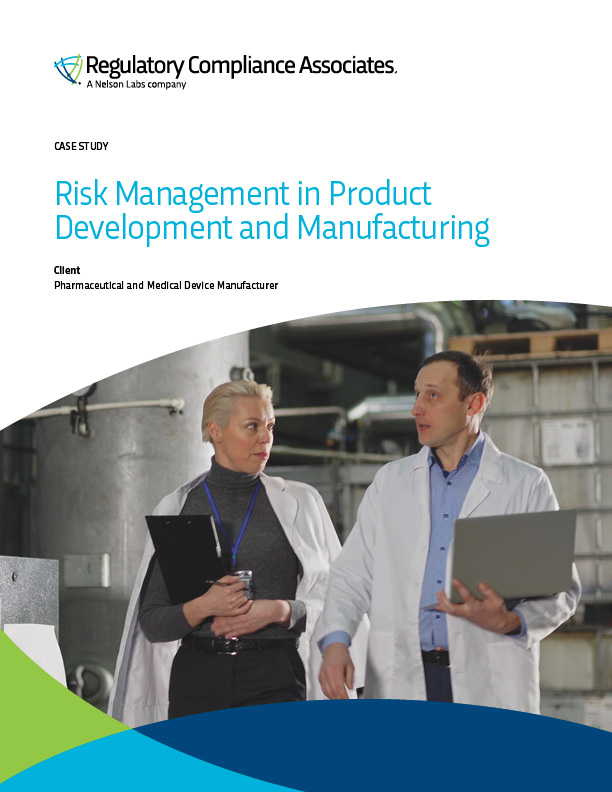
Client
Pharmaceutical and Medical Device Manufacturer
Industry
Pharmaceutical, Medical Device
Business Challenge
Create new PDP procedures for both drug and device development
Background
A global pharmaceutical and medical device manufacturer sought to enhance integration of risk management throughout the product lifecycle. The FDA had identified deficiencies related to risk management in several Form 483 observations. Additionally, the company required standardization of its product development process (PDP) across diverse business units and international sites.
RCA Approach
Regulatory Compliance Associates® Inc. (RCA) provided subject matter experts specializing in product development and quality system regulations. RCA authored a comprehensive portfolio comprising more than ten new PDP procedures and over thirty supporting templates, designed to be flexible enough to address drug and device development, design changes, line extensions, and OEM manufacturing. Training sessions were delivered at client locations across the United States and Europe to ensure consistent implementation.
Result
The new PDP process was successfully implemented, incorporating risk management at multiple key stages:
- Risk Management Planning is a part of Design & Development Planning
- Risk Analysis is an input to Verification and Validation test planning
- Risk Analysis via Process FMEA is required for OEM business
- Risk Reports and Risk Benefit Analysis are inputs to Final Design Review
- Risk Analysis and Reports reviewed periodically based on internally generated data and data received from customers (i.e., complaints)